Kumar Balan étudie l'efficacité du grenaillage vibratoire, sa viabilité financière et sa portée commerciale. Son article couvre tous ces aspects grâce aux données fournies par Vibra Finish.
Dans le numéro d'hiver 2018 de The Shot Peener, nous avons abordé deux techniques de grenaillage non conventionnelles ; l'une d'entre elles était le grenaillage vibratoire. Outre l'état de surface supérieur, nous avons appris que la couche de compression était plus profonde avec le grenaillage vibratoire par rapport au grenaillage conventionnel. grenaillage de précontrainte. Le processus lui-même était sensiblement différent du grenaillage conventionnel en termes de durée de vie des supports, de production de poussière et de coûts des services publics. Nous en avons conclu que cette technique de génération de contraintes de compression résiduelles méritait d'être explorée plus avant. Les résultats sont discutés ici.
Vibra Finish, une société basée à Mississauga, Ontario (Canada), a mené de nombreuses études pour valider les faits établis et définir clairement les limites de ce procédé de grenaillage. Elle a tenté d'identifier les composants, tant industriels que domestiques, qui exigent et peuvent bénéficier d'une combinaison de résistance à la fatigue et d'une finition de surface supérieure, le tout en une seule étape.
Lors de l'examen d'un nouveau procédé, en particulier d'un procédé qui simule une technique établie mais avec des améliorations notables, le scepticisme est courant. Les doutes portent notamment sur l'efficacité technique du procédé, sa viabilité financière et sa portée potentielle sur le marché. Notre discussion couvrira tous ces aspects grâce aux données fournies par Vibra Finish. Étant donné que Vibra Finish opère de manière conventionnelle grenaillage de précontrainte En outre, notre discussion est enrichie par la comparaison des deux techniques avec des variables de processus identiques.
Contexte
La finition vibratoire est un processus primaire à part entière et parfois un processus supplémentaire utilisé pour polir une surface grenaillée. En tant qu'opération secondaire, elle permet d'éliminer la rugosité de la surface créée lors du grenaillage. Une rugosité de surface supérieure à une certaine valeur dépendant de l'application peut avoir un effet néfaste sur la durée de vie en fatigue du composant. Comme nous le savons, la plupart des spécifications limitent l'enlèvement de matière lors de la finition après le grenaillage à 10% de la valeur d'intensité "A". La finition vibratoire peut être contrôlée pour rester bien en deçà de cette tolérance. La finition vibratoire est également utilisée pour l'ébavurage, le brunissage, le décalaminage et est idéale pour la finition des pièces avant la peinture, le placage, le traitement thermique, l'anodisation ou simplement pour obtenir une excellente finition finale.
La finition vibratoire est considérée comme un processus de "finition de masse" et, lorsqu'elle est bien conçue, elle permet d'obtenir un lot de pièces traitées de manière uniforme et cohérente. Le processus ne dépend pas des compétences de l'opérateur, contrairement à d'autres techniques telles que le polissage, le limage, la courroie, etc. Au lieu de cela, un lot de pièces est chargé en vrac dans un bac ou acheminé en continu vers une machine vibrante pour un fonctionnement en ligne. Le bac est rempli de produits de finition et de composés appropriés qui, une fois combinés, agissent comme des milliers de petites surfaces de limage qui frottent les pièces. Le composé facilite l'action de nettoyage et de finition du support (généralement en céramique). Le choix du composé dépend du matériau à traiter, de la finition de surface souhaitée et des exigences propres à l'application et au processus. Les additifs contenus dans le composé peuvent avoir d'autres fonctions telles que le nettoyage alcalin, le brunissage acide, le lavage et l'inhibition de la rouille.
Comme tout autre procédé, la finition vibratoire comporte des variables contrôlables qui modifient la qualité de la finition. Deux des principaux facteurs sont l'amplitude et la fréquence des vibrations. Compte tenu des avantages de ce procédé, il est naturel d'étendre la gamme d'applications de la finition vibratoire afin d'obtenir un produit grenaillé et fini en une seule étape.
Recherche antérieure
En 2016-17, le Dr Hongyan Miao et le Prof. Martin Levesque de Polytechnique Montréal ont étudié les améliorations de la durée de vie en fatigue d'un certain type d'alliage en utilisant le grenaillage conventionnel et le grenaillage de précontrainte. Les résultats de cet essai ont été suffisamment encourageants pour que des tests supplémentaires soient effectués. Les détails de ces essais sont les suivants :
- Conventionnel grenaillage de précontrainte a été réalisée dans une machine automatisée à air avec une buse de V2″ de diamètre propulsant des billes de céramique Z425 sur le composant. L'intensité cible était de 8A, obtenue avec une pression d'air de 20 PSI et un débit de 10 lb/minute. La pièce a été fixée sur une table rotative.
- Le grenaillage vibratoire (ce terme est utilisé pour signifier le seul but de cette opération - le grenaillage) a été effectué dans une cuve de type discontinu remplie de billes d'acier au carbone AISI de type 1018 de diamètres 1/8″, 3/16″ et Vi", représentant un poids total de près d'une tonne. L'intensité de la cible est restée inchangée à 8A comme dans la machine de grenaillage conventionnelle.
- Il est intéressant de noter le mélange de tailles de médias dans ce processus par rapport au grenaillage de précontrainte conventionnel où l'on s'appuie sur une taille de média constante, au point d'utiliser des tamis classificateurs pour maintenir la même taille dans la machine. En raison de la nature exclusive de ce procédé, il n'est pas possible d'obtenir plus de détails sur l'utilisation de médias de tailles différentes. Une explication raisonnable serait de considérer le mécanisme de mouvement des médias dans une cuve de type discontinu, et l'interaction d'une taille avec une autre, comme sur une table de billard. Cette méthode est comparée à celle du grenaillage de précontrainte conventionnel, dans lequel un flux continu d'abrasifs frappe la cible.
- Les deux types de supports (billes en céramique et en acier au carbone) étaient d'une dureté comparable, de l'ordre de 60 HRC.
- Contrairement à l'approche conventionnelle grenaillage de précontrainte Alors que la pièce tournant sur la table était ciblée par l'abrasif, la pièce dans le bac vibrant était positionnée à 10″ sous la surface du lit de billes avec un contact constant des billes en acier au carbone.
L'équipe a tracé des courbes de saturation en utilisant des ensembles de données obtenues par les deux techniques de grenaillage et, avec leurs paramètres de processus distincts, ils sont arrivés à une intensité de 8,3 A et 8,6 A avec le grenaillage de précontrainte et le grenaillage vibratoire respectivement. Les mesures de contraintes résiduelles effectuées sur les pièces testées à l'aide de la diffraction des rayons X ont donné des résultats intéressants. Le grenaillage de précontrainte a produit une surface plus importante et une contrainte résiduelle de compression maximale (-212 MPa et -297 MPA respectivement), par rapport aux -148 MPa et -225 MPa produits par le grenaillage vibratoire. Cependant, la différence se situe au niveau de la profondeur de compression. Le grenaillage de précontrainte vibratoire produit -50 MPa à 520 microns sous la surface, alors qu'avec le grenaillage de précontrainte, la même contrainte résiduelle, -50 MPa, ne s'enfonce que de 340 microns dans la surface. En pratique, si nous sommes en mesure de modifier les paramètres du processus de grenaillage vibratoire de manière à générer la même amplitude de contrainte de compression que le grenaillage de précontrainte, nous pouvons nous attendre à ce que cette contrainte s'étende sur une plus grande profondeur qu'avec le grenaillage de précontrainte. grenaillage de précontrainte.
Les résultats de la rugosité de surface étaient conformes aux attentes. L'étude a comparé la rugosité de la surface de l'échantillon tel qu'il a été usiné, grenaillé et après le grenaillage vibratoire. La rugosité a été testée sur trois échantillons, à trois endroits différents, et la tendance était la même dans tous les cas. L'un de ces résultats est présenté ci-dessous par souci de concision.
Les essais de fatigue réalisés dans le cadre de cette étude ont donné des durées de vie moyennes similaires pour les deux procédés. Cependant, ils ont constaté que les valeurs de grenaillage de précontrainte présentait un écart-type nettement inférieur (variation minimale). L'étude a conclu qu'au lieu de comparer des valeurs d'intensité Almen similaires, les études futures devraient comparer les mesures de la durée de vie en fatigue pour des profils de contraintes résiduelles similaires, à différents niveaux de rugosité. En fin de compte, la mesure de tous ces processus est basée sur la mesure dans laquelle la durée de vie en fatigue a été affectée, de préférence dans le sens positif.
Composants commerciaux et grenaillage vibratoire
Encouragé par les résultats des essais précédents, Vibra Finish a poursuivi avec des essais comparatifs sur des composants plus conventionnels - une pale de turbine et un engrenage de transmission automobile. Les essais devaient permettre d'étudier les points suivants :
- Comparer les effets du grenaillage de précontrainte et du grenaillage vibratoire sur (a) des géométries ouvertes et (b) des géométries relativement fermées afin de connaître les limites que présentent certains types de pièces pour ce procédé.
- Rugosité de la surface
- Contrainte résiduelle et nature des courbes (relâchement de la contrainte de compression mesurée dans la profondeur de la pièce)
Le processus conventionnel de grenaillage de précontrainte a été réalisé dans une machine automatisée à jet d'air selon les paramètres suivants : Intensité de la cible : 10 à 12A et couverture de 100%. Ceci a été réalisé en utilisant de la grenaille d'acier de dureté régulière SI 10 propulsée à 30 PSI par une buse de diamètre Vi" à une distance de sécurité de 8″ pendant un cycle de 30 secondes.
Le grenaillage vibratoire a été réalisé avec des billes d'acier de 3 mm de diamètre, dans une cuve de type discontinu, pour un cycle total de 10 minutes. Deux ensembles de données, l'un pour la rugosité de la surface et l'autre pour la contrainte résiduelle (par diffraction des rayons X) ont été analysés.
Données de rugosité de surface :
Les résultats de l'état de surface montrent une tendance intéressante pour un composant à géométrie relativement fermée (engrenage) par rapport à l'aube dont les surfaces sont larges et ouvertes. La section du pied de l'engrenage, qui est la zone de concentration maximale des contraintes, est la région la plus importante pour les mesures. Dans cette région, le composant grenaillé présente un état de surface beaucoup plus rugueux qu'un composant vibro-grenaillé identique. Toutes les autres régions de l'engrenage, telles que la face d'entraînement, la face de côte et l'extrémité, présentaient des valeurs de rugosité de surface comparables dans les deux procédés. La géométrie de la dent de l'engrenage, l'accès au média et la taille du média sont autant de facteurs qui ont pu contribuer à la valeur finale de la rugosité lors du grenaillage vibratoire.
Bien que le S110 ait été parfaitement adapté au grenaillage du plus petit rayon de la dent d'engrenage sans causer de problèmes de couverture, la rugosité de la surface s'est avérée beaucoup plus élevée qu'avec le grenaillage vibratoire. Cependant, il faut tenir compte du fait que pour atteindre la même intensité (8 à 12A), le S-110 aurait dû pénétrer plus profondément que les billes de 3 mm du vibro-ponçage, ce qui aurait donné un profil de surface plus rugueux.
Une étude du profil des contraintes résiduelles a permis de mieux comprendre les caractéristiques des deux procédés pour induire une compression dans les pièces.
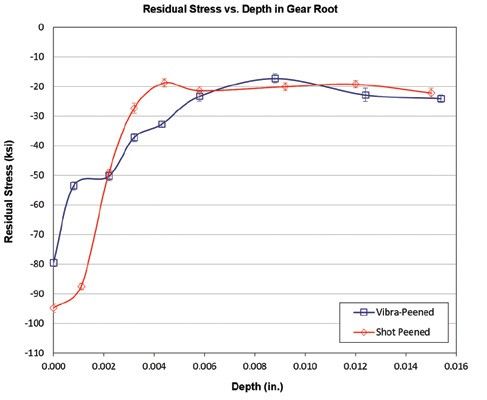
Engrenages
La courbe de contrainte résiduelle pour ce composant est différente de la courbe classique en "J" à laquelle on s'attendait avant d'obtenir les résultats. En outre, il s'agit d'un composant cémenté qui ne présente pas nécessairement des valeurs élevées de contrainte résiduelle lorsqu'il est grenaillé avec un média de taille SI 10 à une intensité relativement plus faible (8 à 12 A). Bien que la contrainte résiduelle à la surface de l'échantillon grenaillé soit plus importante que celle obtenue avec le grenaillage vibratoire, la dissipation (ou la perte) de la contrainte résiduelle vers la profondeur du matériau est beaucoup mieux contrôlée avec l'échantillon grenaillé par vibration. Le grenaillage vibratoire a enregistré une lecture apparemment anormale lorsqu'il a été mesuré à 0,0008″ de profondeur, enregistrant une chute 33% abrupte de -79 ksi à -53 ksi avant de continuer avec une baisse contrôlée et progressive à des niveaux plus profonds dans l'échantillon.
Une question évidente qui reste à évaluer est de savoir si l'état de surface (rugosité) a été la cause de cette chute brutale de la contrainte résiduelle dans l'échantillon grenaillé, surtout si l'on considère la surface plus lisse après le grenaillage vibratoire. La cémentation de l'engrenage peut également avoir conduit à l'ampleur relativement plus faible de la contrainte résiduelle en utilisant les deux types de techniques de grenaillage.
Lame
Une pale de roue de turbine a été choisie pour sa géométrie ouverte. Il s'est avéré que la contrainte résiduelle résultante suivait le schéma familier du crochet en J. De manière surprenante, la contrainte de compression générée à la surface était plus importante avec le grenaillage vibratoire qu'avec l'échantillon grenaillé. Une fois encore, la géométrie ouverte de la pièce et les propriétés du matériau (plus souple que l'engrenage) sont probablement à l'origine de ce résultat. Une observation intéressante est à faire à la profondeur de 0,0021″ où les deux procédés enregistrent la compression maximale. En supposant que la pièce grenaillée ait développé un profil rugueux après le grenaillage, si l'on devait la polir de 10% de la valeur d'intensité 'A', c'est-à-dire 0,0011″, on obtiendrait une valeur de contrainte résiduelle plus élevée (environ -140 ksi) à la surface de la pièce grenaillée. À cette profondeur, la pièce vibrée aura une contrainte résiduelle de -13 ksi sans qu'il soit nécessaire de la polir.
- La chute de la contrainte résiduelle à mesure que l'on s'enfonce dans le composant a été radicale avec la pièce grenaillée et a suivi une diminution progressive avec le composant vibré. Il s'agit d'une caractéristique positive de ce dernier procédé.
- Dans les deux cas, il semble que la géométrie de la pièce ait joué un rôle important dans l'augmentation de l'ampleur des contraintes résiduelles.
Conclusions et étapes futures
Le grenaillage vibratoire est certainement très prometteur car il permet de combiner les deux caractéristiques essentielles de la finition de surface - profil lisse et contrainte de compression - en une seule étape. En outre, dans les deux exemples, on a constaté une dissipation graduelle et régulière de cette contrainte au fur et à mesure que l'on s'enfonce dans le matériau, ce qui prouve que le processus est contrôlable. Les prochaines étapes consistent à étudier les coûts d'exploitation des deux procédés afin d'en évaluer la viabilité financière. Le grenaillage de précontrainte vibratoire ne possède pas le même modèle consommable que celui que nous connaissons tous dans le grenaillage de précontrainte conventionnel. Il en va de même pour les coûts d'investissement liés à l'acquisition d'une machine de grenaillage de précontrainte conventionnelle.
Le grenaillage vibratoire n'est pas encore régi par une spécification. Il pourrait s'agir de la prochaine étape pour accroître l'adoption de ce procédé dans des secteurs connus. Entre-temps, toute une série de pièces de consommation pourraient grandement bénéficier de ce processus combiné.
À propos de Vibra Finish
Vibra Finish, situé à Mississauga, Ontario, Canada, offre une gamme complète de services et d'équipements de finition vibratoire. Ses services comprennent l'ébavurage, le brunissage, le décalaminage, le vibrapeening, le polissage, le dérouillage, le nettoyage, le séchage, la protection contre la corrosion et les services de peening. Visitez le site : vibra.com pour plus d'informations.
Source : L'épluchette de grenaille